Quality-Driven Production
At Goodwood, we believe quality is the cornerstone of our success. For over 30 years, our mission has been to exceed customer expectations, a commitment deeply ingrained in our company culture and reflected in every aspect of our manufacturing processes.
Quality Control Strategy
From Raw Materials to Shipping: Our Comprehensive Quality Control Process.
At Goodwood, our Quality Assurance (QA) strategy is key to upholding the Goodwood brand. Our team of skilled professionals diligently oversees each stage of production. Their commitment ensures that every product meets our strict CTQ (critical-to-quality) parameters. With a proactive stop-fix approach, we promptly address defects before moving to the next production stages. This thorough approach reflects our commitment to delivering high-quality products, emphasizing excellence in every aspect of our manufacturing operations.
From the arrival of raw materials at our facilities, each department diligently upholds their designated CTQ parameters. This meticulous oversight guarantees that every phase of the production process aligns with our rigorous quality standards, culminating in the flawless departure of the final product from our production line. Our dedication to quality extends beyond the end product, as we meticulously package and ship our products to warehouses worldwide. Prioritizing safety and security, we ensure their pristine condition upon arrival, reinforcing our unwavering commitment to excellence throughout every stage of our operations.
Six Sigma Quality Management
The heart and soul of our operation.
Six Sigma is a data-driven methodology used to improve quality and efficiency in manufacturing and service-related processes. The system aims to reduce defects and variation in a process by identifying and eliminating root causes of problems. This is achieved through the use of statistical tools and techniques, as well as a structured approach to problem-solving known as DMAIC (Define, Measure, Analyze, Improve, Control).
At Goodwood, we have integrated Six Sigma into our quality assurance program to ensure that we consistently meet our customers' high expectations and maintain our position as a leader in the industry. This system was introduced in 2019 by Brice, Goodwood’s managing director, who studied quality and engineering at TUM (Technical University of Munich) and is also a certified Green Belt in Six Sigma.
Working with the Best
We believe in working with suppliers who share our commitment to quality and sustainability, ensuring that our customers receive only the best products.
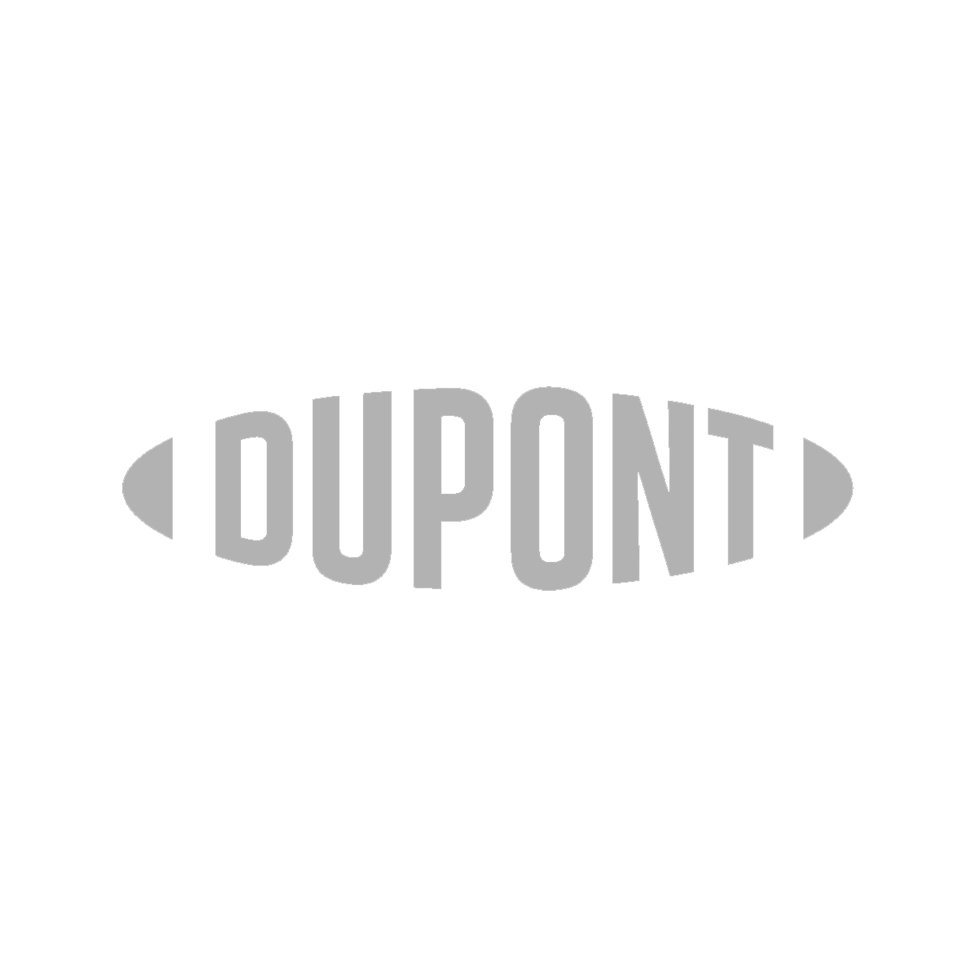
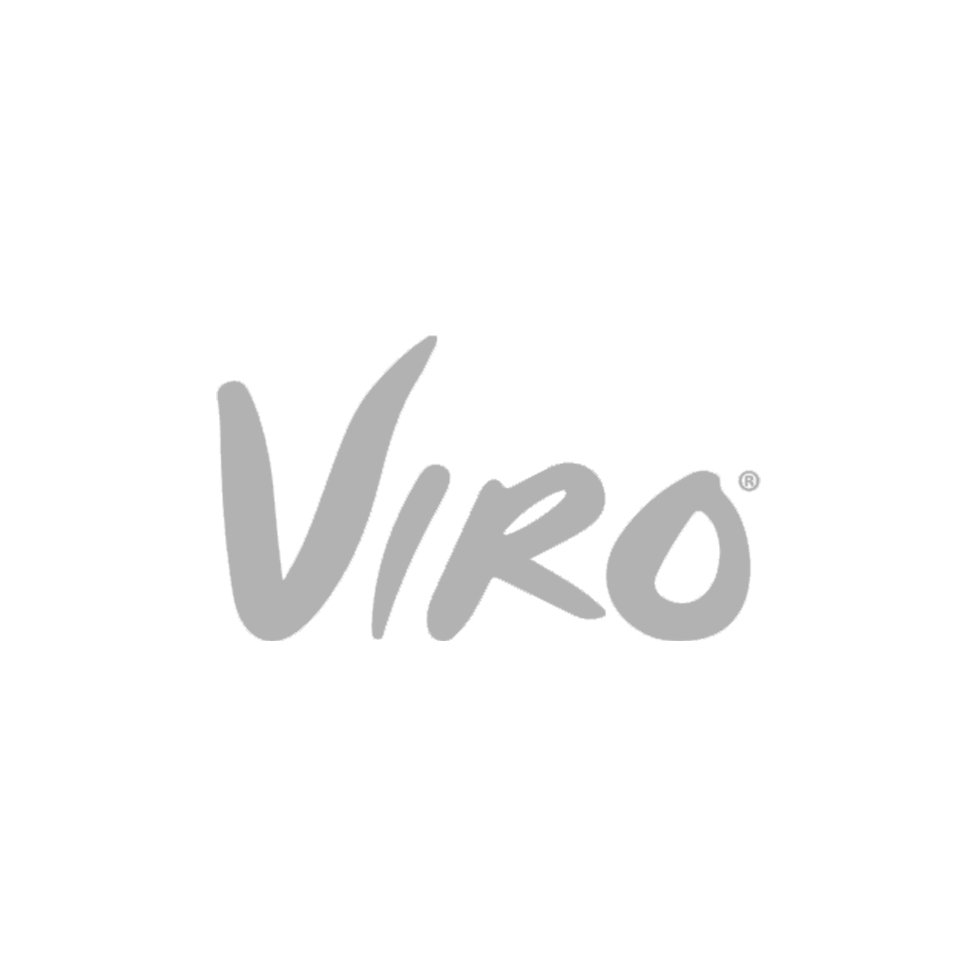
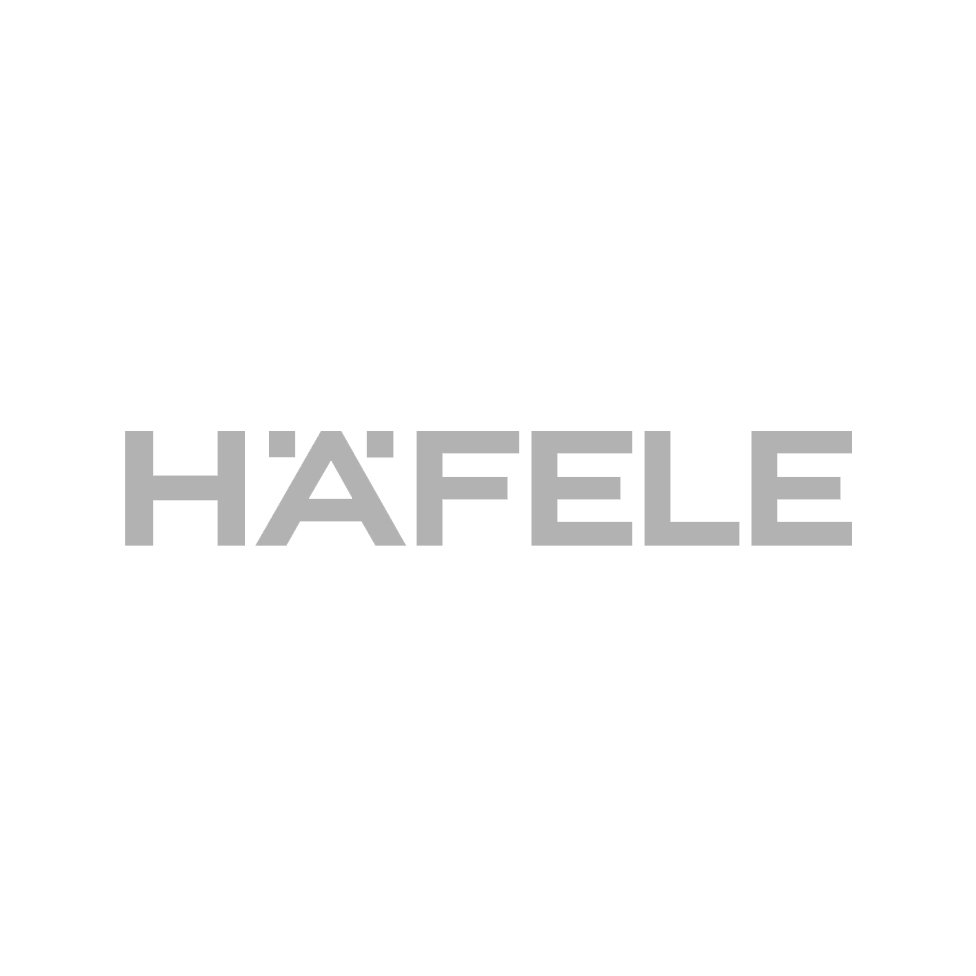
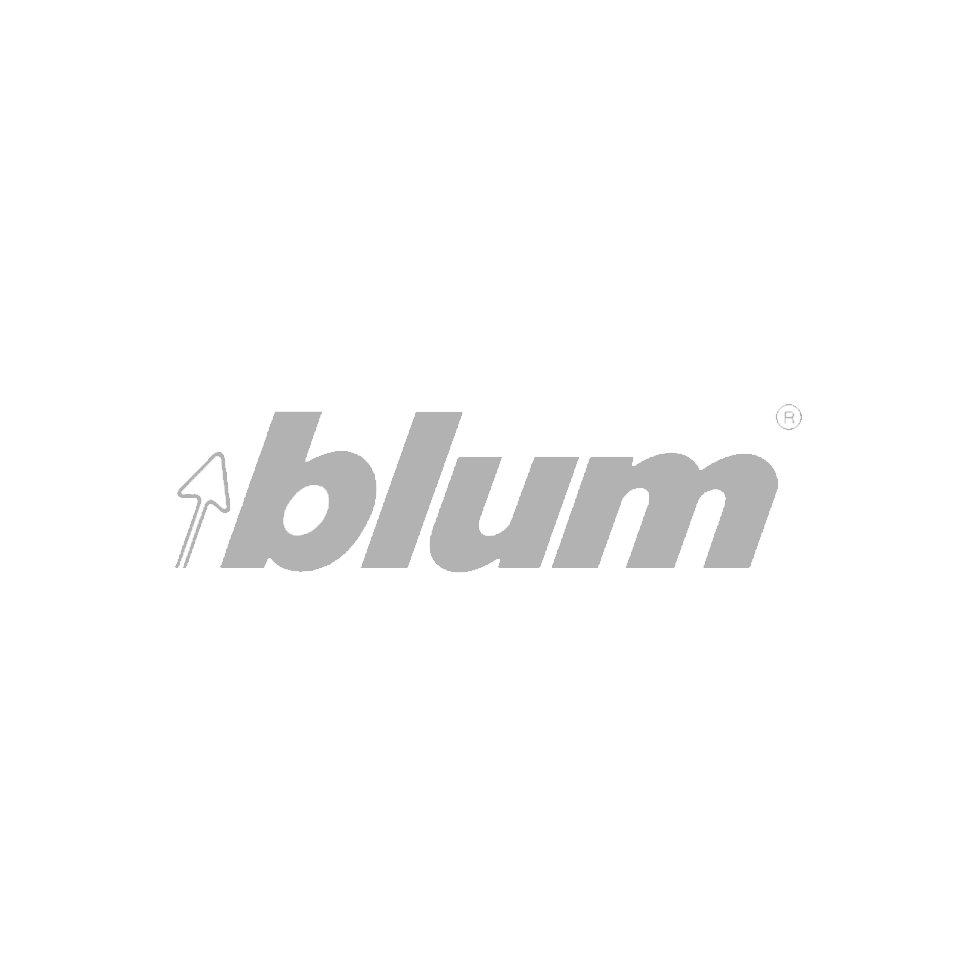



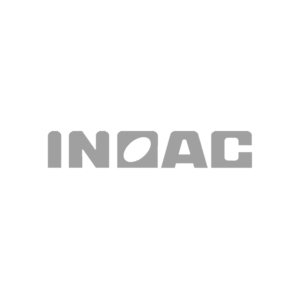




Furniture Testing
Certifying the safety and durability of our furniture products through rigorous testing.
Rigorous testing forms an integral part of our quality control process. To this end, we have partnered with SGS testing, widely recognized as one of the most reliable and respected testing agencies in the industry. Their thorough testing procedures and state-of-the-art equipment are instrumental in certifying the safety and durability of our furniture products.
The testing results we receive from SGS provide us with invaluable insight into the safety and durability of our furniture products. Their comprehensive testing procedures evaluate every aspect of our products, from structural integrity to material composition, providing us with detailed reports on their findings. This allows us to make any necessary improvements to ensure our products meet or exceed industry standards, providing our customers with furniture that they can trust and rely on for years to come. We’re proud to offer SGS certification to our customers, for our manufactured products.
Browse our 2024 Catalogs
Explore yearly innovations from our product and design team, offering a 50/50 mix of new and older products. Our catalogs cover indoor, outdoor, and heritage designs, providing a diverse selection for every preference.
FAQs
-
Our production lead time varies depending on the complexity of the design and the total SKUs in the given order. Our standard production lead time is 70-90 days for a 40ft HC container after we receive the deposit payment. In 2023, our average lead time was 84 days (11.8 weeks).
-
Goodwood’s MOQ is a 20ft container. We accept multiple SKUs in a shipment, however each SKU has an individual MOQ that needs to be met. MOQs are subject to change depending on the order, such as commercial projects.
-
In the event that a product is defective, we will arrange a direct replacement. This guarantee covers all production-related defects, but does not cover faults caused by; transportation, misuse, improper assembly, and intentional damage.